Digitalisation drives manufacturing to the next level
The shift to predictive maintenance key to improving the lifecycle and availability of critical systems
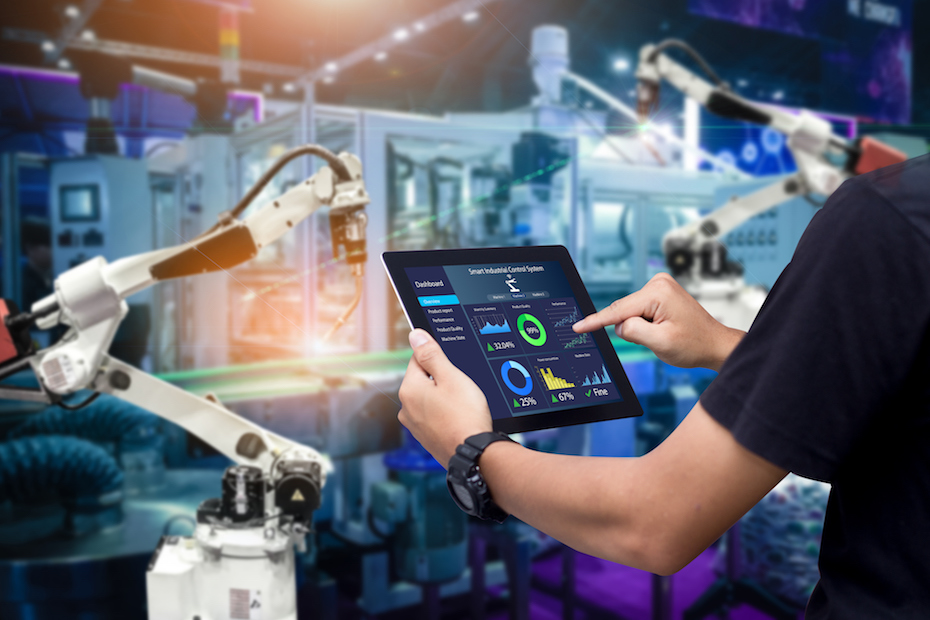
The Fourth Industrial Revolution (Industry 4.0) represents a fundamental change in the way we live, work, build and develop the world. It is playing an integral role in our economies by combining vast developments in digital technology, including machine learning and big data, with physical production and operations. Digital transformation has weaved itself into every aspect of lives with technology creating a lifeline that keeps us connected both personally and professionally. For the manufacturing sector, this has elevated the role of digital technologies to a whole new level.
Most significantly, many major industrial plants are shifting their approach from “owning equipment” to “managing the life cycle of a complete solution”. In strategic complex infrastructures, “availability” has taken over “reliability”. Availability here refers to the percentage of time that the infrastructure, system or a solution, remains operational under normal circumstances to serve its intended purpose.
Owners and users of industrial equipment are no longer looking at the equipment itself but are interested in the service delivered by this equipment. When considering the service delivered, the equipment itself is only half of the equation. The other half, which is also very cost-effective, is the ability to maintain it. This makes maintenance strategies essential to create a more holistic and better-connected ecosystem, particularly for organisations that focus on manufacturing and supply chain management.
This is where the need to shift from preventive maintenance to predictive maintenance comes from. In older processes, much of your time can be focused on operational aspects and less on the lifecycle of the system. By improving the lifecycle, a company will become more competitive by bolstering the availability in an increasingly complex system, which, ultimately, translates into a cost-benefit. Also, by defining a clear lifecycle for the system (including its design, delivery to customers, and the eventual migration to an improved system), maintenance and ease of use are key. By making it more intelligent, it is easier to manage the data and improve the flow of operations over a much longer period, perhaps decades. However, the move to predictive maintenance will only happen when trust in the employed technologies, data and processes is guaranteed.
With predictive maintenance the main objective is to ensure that the system will deliver around the clock, 365 days a year. This means that companies, government agencies, or government-regulated entities can be assured that their whole production, logistics and supply chain, will always be up and running.
As witnessed by the early adopters of predictive maintenance, it is now a crucial and integral role for improving global industrial output. By combining the rapid developments in digital technologies, including IoT, artificial intelligence, power computing, and big data, alongside physical production and operations automation, we can reach high levels of infrastructure delivery and availability with a high level of confidence.
The three core elements to consider when deploying critical system maintenance strategies are: Safety, Security, and Availability. In any given geopolitical territory, Maintenance 4.0 is increasingly key to contributing towards achieving sovereignty and autonomy. In part inspired by its sustainable approach to 21st-century production, to achieve this goal, the UAE has put in place a manufacturing skills strategy that includes cross-domain competencies and vocational training across manufacturing sectors.
When it comes to the implementation of predictive maintenance strategies, government-level projects focused on critical systems such as electricity and water supply, nuclear power, or transportation and logistics, often receive appropriate state funding, however, the costs for private industry, as well as smaller manufacturing entities, may seem daunting. But just as you cannot put the roof on a house without foundations and supports, the same logic applies to scaling up a predictive maintenance approach.
For SME to mid-sized entities, small incremental steps can be taken to transition the company towards Industry 4.0 standards. In such cases, Condition-based maintenance (CBM), integrated across selected priority assets, will demonstrate the value of early warnings on potential failures and establish the foundation for a more comprehensive strategy. The learning experience gained from these initial applications will then dictate how the system can be rolled out across the whole operation and facilities.
In conclusion, introducing a Maintenance 4.0 strategy and Predictive Maintenance cannot simply be achieved through the acquisition of new technology. It must form part of a wider approach of seamless integration between industry, innovation and education. To develop new and disruptive technologies for Maintenance 4.0 with the required level of trust and maturity, powerful research and development capabilities, as well as cooperation with local top-notch innovation ecosystems are basic prerequisites. These will provide the foundation for developing and sustaining a relevant maintenance skills base and a strong dynamic of innovation. That’s how providers of both a disruptive product and its innovative, efficient maintenance will stand apart in a world of giants.
Bernard Roux is the CEO of Thales, UAE